From lumber to drywall to steel to plastics, the cost of construction supplies has been skyrocketing over the past year. Every sector has been affected - throughout the construction industry, asking about the price of materials has become as common as asking about the weather. And while fluctuations in material pricing are not unheard of in construction, this wave is different because there is no clear end in sight. No one is sure when things will begin to stabilize, but savvy companies are coming up with ways to save money and keep building - starting with strategic hiring, alternative building materials, and construction technology.
How Rising Material Prices Are Impacting Companies
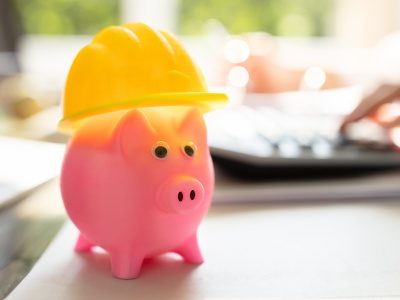
When COVID hit in the first quarter of 2020, many projects were delayed or cancelled due to safety and scheduling concerns. By the fourth quarter of 2020, though, the industry was rebounding and companies were ramping up their construction efforts. Then something unexpected happened: costs started rising. And then they kept rising. Because of smaller staffs and lower productivity during the pandemic, fewer trees were cut and less lumber was produced, resulting in low supply, high demand, and prices that have tripled for that supply. Meanwhile, a catastrophic snowstorm in Texas shut down resin plants, affecting the availability of plywood, PVC pipe, and plastics. And the import of building materials was devastated by a shutdown of major ports at the height of COVID.
Every material that goes into making a building has significantly increased in both demand and price over the past six months - some even doubling or tripling in cost, a budgeting gap that many construction companies are not financially prepared to overcome. Initial estimates for projects have been blown out of the water due to these new prices. When budgets can’t be met, the increased costs of construction are resulting in higher sale prices for all types of developments, perhaps most notably multifamily and single-family homes. Rent and purchasing prices for homes are soaring across the country, at a time when residents are also struggling financially and many aren’t able to pay the higher costs of living. Eventually, developers will be forced to delay projects and stop pursuing new work due to these price hikes, potentially leading to a decreased supply of new construction.
What Companies Are Doing to Combat Rising Costs & Material Shortages
Make Strategic Hiring Decisions
Obviously, the lack of affordable building materials is a significant source of stress for construction companies in every sector. Factories and mines that were affected by COVID are struggling to catch up, but fortunately, most states have lifted lockdown regulations, which means employers are continuing to build strong teams to increase production. In highest demand are skilled Estimators, Preconstruction Managers, and Cost Specialists, whose services can help keep builders on top of constantly shifting budgets as prices fluctuate. These types of candidates often have strong relationships with subcontractors and suppliers so their knowledge and connections within their local market can be invaluable to companies. More generally and in every type of position, companies are seeking out-of-the-box thinkers and skilled problem-solvers; these skill sets are more valuable in this market than ever before, from field labor to the C-suite. Of course, with the ongoing labor shortage, this is not a simple task for many companies, but strategic hiring is an investment that construction companies will never regret.
Build With Alternative Materials
In other cases, contractors are investigating new ways of building that utilize alternative building materials. Examples include organic materials such as rammed earth, mycelium, and hempcrete; reclaimed wood and metal; and recycled plastic. By using these types of materials, builders decrease the amount of lumber required for new construction and renovation projects and thus lower the overall cost of construction. Some companies were already researching the benefits of alternative building materials due to the rise in demand for sustainable construction, but with the cost increases associated with all standard building materials, these alternative options are gaining ground in mainstreaming building.
Cut Costs Wherever Possible
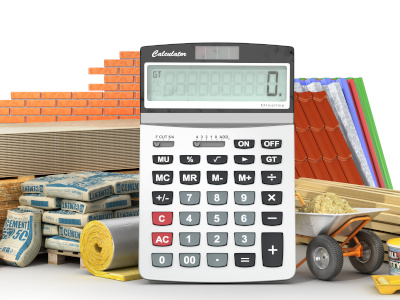
As owners and developers cancel or delay projects until the material cost crisis passes, contractors are focused on keeping their budgets tight in any way they can. For some, this means setting price guarantee dates on their bids, only guaranteeing their estimated costs for a certain amount of time. This helps them react as they market shifts, rather than tying them to a bid price that could sink their profits. Most contractors are still operating with a reduced staff, and in combination with material availability, their bids and budgets must accommodate longer than average building schedules in addition to the higher material prices. Other companies are increasing their use of prefab and precast materials, which has been shown to increase efficiency and reduce overall project costs. And finally, some contractors are utilizing technological advances to help them cut costs, from BIM to 3D printing and drones. There are numerous examples of construction technologies that can help save money - not to mention improving the safety and overall quality of construction projects.
This is an unprecedented situation for the construction industry, and ultimately, there is no way of knowing when production (and thus availability and prices) of building materials will return to normal. But the best thing construction companies can do in the short term is invest in strategic new hires, think creatively about building materials and processes, and keep costs low however they can. The good news is, when things stabilize, these companies will be even better positioned for long-term success.