Supply chains have historically been driven by lean standards, with efficiency as the top priority. Due to the success of lean business models for supply chains, industries from nearly every corner of the world have adopted elements of these standards. But unanticipated internal and external shakeups known as “black swan events” have cast doubt on the efficacy of lean processes. To both reduce risk and sustain efficient practices, industry leaders must stop relying solely on lean. They must also design “flex” into their corporate thinking.
The Rise of Black Swan Events
One of the most significant black swan events in supply chain history, the Fukushima Daiichi nuclear disaster, caused a complete breakdown in Toyota’s supply chain when the sole supplier of a key component was devastated by the disaster. Toyota’s commitment to the leanest possible supply chain resulted in the lack of a failsafe, brought an industry leader to its knees, and launched a reevaluation of corporate policies across the industry. Fukushima was not the first or last event that caught companies unawares, which had significant effects on both global local and markets. Other examples of external black swan events include the September 11th attacks in 2001, the COVID-19 outbreak in 2020, and the rise of technology (including AI, IOT, and machine learning). But black swan events can also come from within organizations, such as the sudden passing of a company’s CEO or a devastating fire at a primary distribution center. Some of these events have short-term impacts, while others can produce unforeseen long-term effects on individual companies or entire industries.
Many of these events cannot be anticipated. Some give warning signs that executives must be cognizant of as they design and evaluate their ongoing corporate strategies. Even when a company cannot plan for an event, they can create contingencies that allow their businesses to pivot when the ground beneath them shifts. At the Board level, many companies have strategies for dealing with internal black swan events, but external events are increasing both in pace and in impact, as business operations are increasingly globalized. To mitigate risk for their companies, executives must think about external black swan events, analyze their potential impact, and plan for their eventuality. Most importantly, they cannot fall victim to these seven fatal words: “But we’ve always done it this way!”
Lean’s Not Dead - It Just Needs Backup
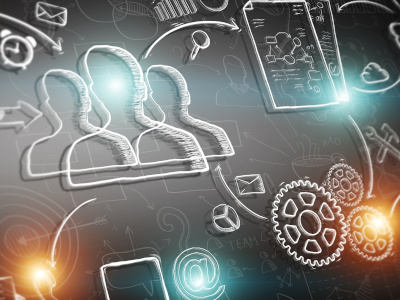
After the Fukushima Daiichi nuclear disaster revealed significant failings in the “lean” model, analysts were quick to make sweeping dismissals: “Lean is dead!” But as is often the case, the truth is not that simple. Lean processes are crucially important in many ways to companies; however, relying solely on lean is a short-sighted strategy. So rather than eliminating a lean mindset altogether, executives should embrace a combined approach. Keeping processes streamlined and efficient can be helpful when things are going smoothly, but companies should also create “flex” backup processes in the event of black swan events that disrupt standard operations.
In addition, leaders can apply “flex thinking” to their hiring and retention strategies. Rather than seeking candidates with siloed expertise, many hiring managers are now pursuing applicants with extra skill sets. For instance, a supply chain planning expert is a stronger hire if they also have some finance expertise. Or consider the versatility and added value that a distribution operations professional with strong IT credentials can bring. These types of flex workers can come when making new hires or when upskilling current employees who are hungry for growth and continuous learning opportunities.
Plan Ahead or Get Left Behind
However a company that has maximized lean today will almost certainly not be the leanest strategy for long, due to the velocity and vectors of local and global market changes. By shifting perspectives from “lean is king” to “flex is power,” executives can broaden conversations within their organizations so that they de-silo existing business units and de-silo the new employees they hire.
A great starting point for leaders who want to shift to flex thinking is this: consider what the company is doing differently today than it did in March of 2020, before the full weight of COVID struck. Every company does something differently, and most companies had few or no plans for those changes at that time. However, the companies that are successfully navigating these murky, turbulent waters managed to find ways to address the challenges that arose, shifting their perspectives and strategies to meet the new needs of their employees, clients, and stakeholders. They pivoted. They flexed. And they survived.
***The next installment of this series will focus on the importance of hiring skills “translators” and de-siloing business units and employees.